ShopEdge ERP Software
ShopEdge offers a comprehensive ERP Software solution for Metal Stamping and repetitive manufacturing environments with a strong shop floor focus.
The scheduling engine extends visibility and control over the entire shop floor. You can view scheduling in detail and control materials, equipment and labor. Then quickly evaluate performance and accommodate additional requests for production or take advantage of production gaps. You are alerted to changes and the impact can be viewed well into the future.
Stampers become responsive to changing demand and have precise capacity planning capability. They also have predictive power allowing them to be proactive or simply “get ahead” and are empowered to fulfill current and future production targets with ease.
- Live shop floor view; see what jobs have started, are in progress, have ended, and have ended unsuccessfully due to tool break, material shortage, etc.
- Compare your schedule plan to actual production execution with our “performance baseline”
- Easily modify items on the schedule; move jobs to alternate workcenters, modify quantities or insert new jobs without having to enter a customer order
- View our Capacity Planning screen to plan for the future of your Metal Stamping business based on historical and forecasted orders
- Integration with Tooling, Equipment and MRP modules allows planners to manage all variables when putting together the production plan
With inventory automation, data collection occurs at network speed using proven technologies. Granular detail on all inventory positions is presented; you don’t need to wait to see what is occurring.
Complete traceability is automatic and precise detail on all inventories, inside and outside, is immediate. Simultaneous inventory decrement occurs with production ensuring inventory accuracy. Inventory automation results in clear visibility and exacting control of your inventory volumes for smart and timely changes across your enterprise.
- Complete raw material, work in process (WIP), maintenance repair operations item, and finished goods inventory management
- Visibility into Outside Processor inventory; raw, WIP and finished goods
- Inventory management for multiple warehouses and production facilities
- Serialized inventory management ensures complete traceability of all manufactured and raw material items
- Double inventory count (barcode and production inventories) results in more inventory accuracy and reduced cycle counts
ShopEdge Software’s powerful mobile application suite offers a wide variety of mobile solutions for stampers. Our suite has full shop floor functionality targeting a wide range of mobile devices from handheld and forklift terminals to Android™ devices and Smartphones. Modules include: Shop Floor Control with Workcenter Management, Quality Assurance, Inventory Management with WIP Tracking, Physical Inventory and Cycle Counts, and Shipping & Receiving.
Our wireless application has been redesigned and enhanced to function on Android™ Smartphones and Tablets. The new, native mobile version of our application can be accessed on any type of Android™ mobile device. Impressive new features empower managers and shop floor employees by providing simplified data entry and easy access to decision making metrics.
The ShopEdge Android™ Application allows end users to access actionable data with quicker response times resulting in decreased downtime, better customer service, and increased employee productivity all while maximizing your hardware investment. Visit our Resources page for more information.
- Full integration into ShopEdge ERP Software using your preferred hardware or Android™ device
- Increased enterprise-wide communication and productivity
- Easy to navigate user interface
- Accessible on all types of devices on the Android™ mobile operating system, as well as handheld mobile computer devices & forklift terminals
- Increased customer service due to quicker response times
- Real-time access to workcenter and item production information including efficiency, inventory, quality and downtime information
- Enhanced productivity in Production, Quality, Shipping & Receiving and Tooling & Equipment as users are able to view and easily enter information in the application
- Maximize your hardware investment with support for a wide range of mobile devices
- Customer and vendor EDI order and shipping communication
- Easily scan receive raw material against vendor ASNs
- Customer-owned and internal container management
- Complete outside processor inventory control
ShopEdge’s Material Requirements Planning is the ultimate MRP module. Coordinating materials with production, the MRP incorporates up to the minute production information to offer real time insight into what is required.
You also see which materials are required to meet upcoming production targets. Material shortages or issues are easily identified so planners can take appropriate and proactive measures to resolve any issues before they become problems.
- Integration with customer releases and production allows you to view the most up to date information in the system
- Let the system automatically replan your materials to meet your schedule or order demand
- Easily view materials that are short for scheduled and planned and production runs
- Send purchase orders and/or releases to your vendors via email or EDI
With an objective of providing a competitive advantage, we are focused on delivering business insight that originates from your source data. Our insistence in collecting this granular level source data and then presenting it in easy to use formats is what sets us apart. Source data is the foundation for informed decision support. Critical data is presented in information rich screens, reports and dashboards.
ShopEdge Reporting is completely customizable, offers multi-layer views and drill down features and can be delivered to your inbox automatically. Similarly, ShopEdge Dashboards go beyond typical executive dashboards by allowing you to preference the views and then drill down into areas of interest and opportunity. This easy identification of source data and areas of opportunity enable the enhanced business decisions needed for Continuous Process Improvements and to deliver a competitive advantage.
- Simple to view graphs, with the ability to drill down to specific source details
- Report building tool allows for custom report development
- Compare progress against historical and target data all on the same graph to clearly measure achievement
- Functional dashboards allow user to quickly navigate to information in the system that needs attention
- Stay above the competition using an extensive library of industry-specific reports with multiple levels of detail to drive important decisions
Tooling & Equipment Maintenance is integrated with the Production Module for seamless shop floor communication. Coordination of tooling and workcenters is automated enabling improved Overall Equipment Effectiveness (OEE). Decrease downtime by scheduling Preventative Maintenance (PM), and tracking all maintenance work to tools, presses and components.
Effectively view and schedule changeover dies right on the Production Schedule, and create work orders for the Tooling or Maintenance Departments immediately.
- Link one or more tooling items to job operations
- Link multiple job operations to a single die
- Integrated with the production system to show tooling availability
- Tooling repair requests/alerts to be generated by workcenter operators and sent directly to the Tool Room Manager
- History of repairs including Work Orders and MRO Items consumed
- Scheduling maintenance for tools and equipment by piece count, one-time, or recurring
- Viewing overdue and upcoming maintenance
- PM Program is easy to set up & automatically updated by reported production
- Attaching MRO items to tooling items; MRO inventory and purchasing
ShopEdge is a “point to point” EDI trading partner and supports both the domestic and international standards. Customer and Vendor unique EDI and Advanced Shipping Notifications (ASN) protocols and specialized printed forms or documentations are used for flawless interactions. We are EDI certified with GM, Ford, Chrysler and many other trading partners.
- Complete plant locations, and contact management
- Automatically print shipping paperwork, including export documents
- Send ASN and in-transit details via EDI or email
- Receive Shipping Schedules and Planning or Forecasted Schedules
- Reports to show weekly customer release changes
Metal stampers often need to send materials off-site for further processing. Inventory must be tracked going to/from a processor, and lead times must be considered when scheduling jobs.
Our processor system pays special attention to outside processing, incorporating processor-specific features as an integral part of our package, from production, and purchasing to shipping, and inventory control.
This material at a processor is tracked as a separate inventory in the system giving production and material planners clear visibility of the location and status of materials.
- Bill of material for outside process operation, allows for the consuming of materials at the processor
- Ship raw material and track inventory at your processors
- Automatic scheduling of quantities to ship to processor considering vendor lead time
Barcoding is an integral part of the ShopEdge system, from handling customer-specific label requirements for shipped goods, to simplifying inventory control. Barcoding reduces errors and simplifies data entry tasks.
Complete barcoding design and bar code printing capability is an integral part of the system. No additional requirements are needed. The system is hardware agnostic, incorporates generic symbologies, includes AIAG templates and handles customer specific labeling reducing errors and simplifying data entry tasks.
- Mobile and Android™ applications allow for easy shop floor management
- Design container, shipping, address, master and customer specific labels in the system
- Print customer specific labels at the time of production for effortless processing in shipping
- System generated serial numbers printed on barcode labels ensures simplified inventory management
ShopEdge Software has bridged the gap between ERP software and the shop floor with the introduction of our new Machine Integration module. This module eliminates cumbersome and error-laden data entry by pulling important production information directly from any machine, with or without a PLC device.
See your shop floor in real-time with our new Shop Floor Monitor. Valuable production information is captured straight from the shop floor to feed the highly visual, information rich display. It is easily accessible anywhere from a web browser, or directly from our Android™ application.
- Automatically populate valuable production data with minimal operator input
- Integrate with any machine, either directly with a PLC, or using intermediate hardware
- Know exactly when machines are down, why they are down, and troubleshoot recurring issues
- Gain access to granular machine data to help improve OEE
- Improve production efficiency and maximize resources
- Benefit from an extensive library of production reports that enable company decisions to improve profitability
The uninterrupted flow of financial data into our comprehensive financials, General Ledger, Accounts Receivable and Accounts Payable removes inaccuracy, eliminates delay and speeds reporting. You can organize the chart of accounts in your hierarchy and run month end closing “on demand”.
Complete journal entry capability, multi currency and more is included. The full financials include a custom financial statement reporter plus our Business Intelligence Reporter. All the financial information is in one location and ready for detailed review and reporting with a few keystrokes.
- Check and various payment printing and processing, including pushing ACH and wire transfer files directly to your bank
- A/P directly integrated with receiving, ensuring accurate invoice posting
- Send XML financial information directly to the government of Mexico for monthly review
- Complete control over financial statements designed using our ShopEdge Financial Reporter
Focused on item level quality, specifications and materials are strictly monitored. Quality disposition status is quickly assigned for efficient Q/A processing. Quality responses incorporate your procedures and personnel.
Integrated Quality Inspections at each operation with flexible deployment options allow operators or Q/A personnel to complete inspections during production, and immediately analyze results using measurement history and charts.
Complete traceability at all levels of production supports quick responses and scheduled Statistical Process Control (SPC) minimizes quality issues. Pragmatic quality management compels ongoing communication across departments for quick action to maximize first time item quality.
- Easily process and track customer and vendor returns, or internal rejects in the system or by using the mobile suite for simplified data entry
- Maintain material specifications, chemical and physical properties and complete heat tracking and traceability from raw materials to finished goods
- Create quality inspection templates to be completed on the floor at each operation, and review and analyze data via charts and graphs
- Gage calibration module allows you to manage gages, track calibration procedures and record R & R studies as part of your quality certification requirements
APQP handles all of the intricate planning phases for product launch. Critical milestones such as Production Part Approval Process (PPAP) dates are achieved with improved project control. The APQP system boosts co-operation between departments by allowing tasks to be linked and facilitates the approval process.
- Support for PPAP dates and quantities
- Tracking of revisions against jobs
- Emailing reminders directly from a task
- Tasks organized by department
- Tasks due dates are relative to either PPAP or Job Issued date
- Full audit on task changes
- Unlimited user comments and attachments against a task
- Full integration with ERP system to eliminate data duplication
- To-do list of tasks with user-defined queries
- Adding pictures and external documents (eg: CAD drawings) to jobs
NEW PRODUCT: ShopEdge Unified Application
The ShopEdge Unified Application is the latest release in our application suite, bringing together our shop floor and business enterprise functionality into a single application. The application is developed using Microsoft’s Blazor, an open-source application framework that can run in any web browser or as a native client application on most devices, providing extremely fast, almost native performance using a desktop or mobile form factor. And because Blazor is a modern front-end framework based on web standards, we can develop features quicker in an application with a beautiful user experience.
Find out more information by downloading our Unified Application flyer here.
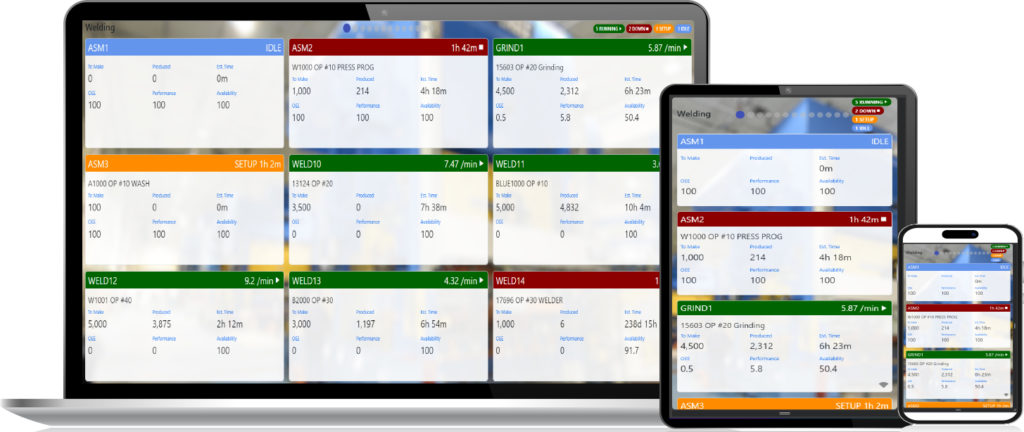